Clearing Up Questions about Soda Ash, Make-Up Water
Are There Alternatives? Can it Make pH too High?

Those who mix fluids in the field can benefit from arming themselves with testing basics for water pH and hardness.
Source: Getty Images
The industry considers soda ash the go-to product for pre-treating water for mixing drilling fluids or slurry, whether for water well, geotechnical or horizontal directional drilling, or for foundation drilled shafts. Training seminars for drilling fluids or slurry always teach the virtues of pretreating with soda ash. However, amid all the virtues, users could naturally have a few questions.
- Why use soda ash in the first place?
- Is there a product to use in place of soda ash?
- Even though soda ash produces a maximum pH of only 10, can we “overdose” with it in our water?
- Are there times we do not need to add soda ash?
This article will answer these questions and, hopefully, help drilling contractors make more-informed decisions regarding the use of soda ash for drilling fluids or slurries.
Drilling Fluids, Slurries: Why Pretreat the Water?
On the jobsite, we use soda ash to pretreat water, raising pH to 8.5 to 9.5 — just over neutral into alkaline — before mixing bentonite or polymer. Soda ash also precipitates calcium, which is part of what gives water its hardness. Softer is good. Calcium levels above 120 ppm and salt/sodium levels 1,000 ppm hamper both bentonite and polymer drilling fluids or slurries. Bentonite flocculates and settles out of suspension. Polymer drilling fluids or slurries break down.
Use soda ash in moderation to avoid raising salt/sodium contents above the tolerance levels of bentonite and/or polymers (overdosing).
We also pretreat water to increase bentonite dispersion. Many people fail to realize soda ash (sodium carbonate, Na₂CO₃) is a salt formed by carbonic acid and sodium. Therefore, use soda ash in moderation to avoid raising salt/sodium contents above the tolerance levels of bentonite and/or polymers (overdosing). Normal dosage for soda ash ranges from ¼ to ½ pounds per 100 gallons of water. Always start at the lower dosage. Utilize pH test strips to prevent overdosing and shoot for a pH of 8.5 to 9.5.
Raising the pH can increase the rate at which both bentonite and polymers hydrate and build viscosity. This stems from increasing the overall negative charge. However, with otherwise fresh mix water, you may see lower ultimate viscosity from your polymers as the balance to the faster viscosity buildup.
Alternatives to Soda Ash in Fluids, Slurries
Soda ash pretreatment, as I’ve established, has its virtues. But you may wonder about alternatives that do a similar job.
The oilfield drilling industry commonly uses caustic soda (sodium hydroxide, NaOH) to increase pH to neutralize and to precipitate calcium and magnesium. Caustic soda excels at treating hard water, especially when magnesium is present. Unfortunately, caustic soda has an extremely corrosive pH of 14. Handling it without proper PPE (or incorrectly used PPE) can cause serious injury. Caustic soda helps in foundation drilled shaft applications when you encounter organics (think bio matter like peat moss). When drilling into these conditions with a synthetic slurry pretreated with soda ash, the pH and viscosity can drop. Caustic soda can maintain pH and viscosity, but take the necessary precautions and avoid letting the pH get too high (overdosing over pH 11 or so).
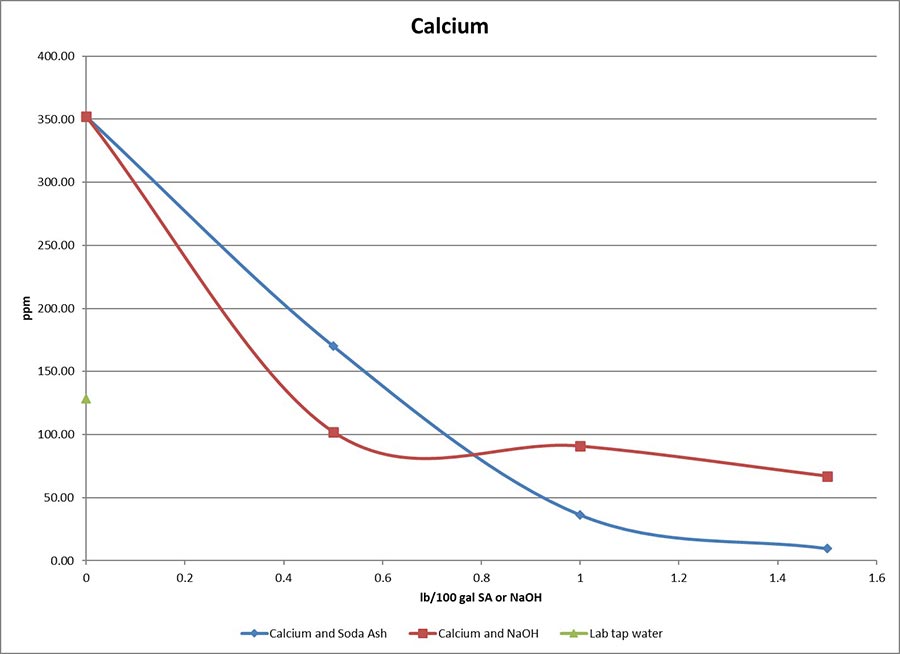
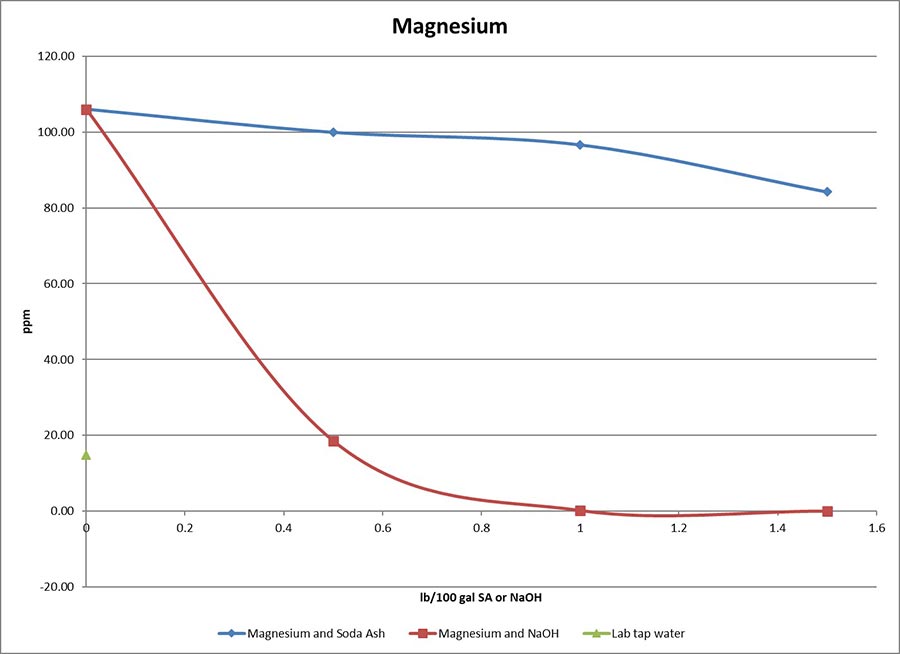
Source: CETCO Drilling Products
You also often see sodium bicarbonate (aka, baking soda, NaHCO3) used in drilling fluids and/or slurries to combat cement contamination. In this situation, viscosity drops and you see an increase in pH (often over 11). Sodium bicarbonate can buffer the pH of cement-contaminated drilling fluids or slurries, reducing them from a pH of 12 or 13 down to a better range of 8 to 9.
As far as subbing out your soda ash for baking soda, my colleague Greg Plutko, a research scientist at the CETCO Lab in Hoffman Estates, Illinois, has studied this. He says sodium bicarbonate “treats out hardness well enough although a slightly higher dosage is required than with soda ash.” He adds that, “The pH would max out at about 8, as opposed to the 9 or 10 that you get with soda ash. This means that bentonite might be slightly slower to hydrate, but not too slow, as the pH is still in the range that benefits our clay. Sodium bicarbonate, in most cases, just acts like a slightly less effective soda ash unless you are trying to bring the pH down from above 11 (as is the case with cement contamination).”
When Not to Treat with Soda Ash
As mentioned, pretreating mix water is not always necessary. If the calcium content of water is 120 ppm or less, soda ash is not required. This is especially true when mixing synthetic (polymer) slurry, where adding salt may do more harm than good. I always recommend treating out hardness levels higher than about 120 ppm, however. Find water hardness strips at swimming pool supply facilities and some hardware stores, or simply order them online. They give you a quick, easy way to determine the calcium and hardness content of water, which helps determine if soda ash is required.
To check out more of our columns, click here!
As previously mentioned, soda ash is the go-to product for pre-treating water before mixing bentonite or polymer drilling fluids or slurries. But use it correctly and in moderation. Utilize water hardness strips to test for calcium levels. Use pH test strips to test water pH and pretreat mix water with calcium over 120 ppm. Utilize pH strips to ensure the treated water does not go over a 9.5 pH to avoid overdosing with soda ash.
I hope this clears up some questions about soda ash, and explains its place in building your optimal fluids and slurries.
Looking for a reprint of this article?
From high-res PDFs to custom plaques, order your copy today!