Sonic Drilling, Water Hammer Combo Rig Developed for Dam Projects
Company Calls Drill Prototype a ‘Swiss Army Knife’ for Remediation

A photo of the WS6000 shows some of the features, including the “Rodbot” rod handling arm and enough storage for 600 feet of pipe.
Source: Scott Dalrymple / MEDATech

The Rodbot rod-handling system is similar to what automakers have used on assembly lines for years.
Source: Scott Dalrymple / MEDATech


Passionate, trained engineers and homegrown tinkerers populate the drilling industry. Scott Dalrymple is the former. He worked on a rig that delivered a mashup of down-the-hole water hammer and sonic technologies for client Alabama Power, a division of the Southern Company.
The result was the track-mounted WS 6000.
“Dam rehab is a big market, for sure,” says Dalrymple, design engineer for MEDATech and product manager for their drilling division, Borterra, in Calgary, Alberta, Canada. “This machine’s very versatile. It’s a bit of a Swiss Army knife. There’s not much you can’t do.”
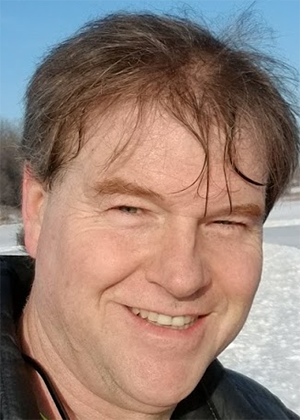
Dalrymple says the WS 6000 helps the driller stay on target. Operators switch between the two modes as needed with the push of a button, giving them the flexibility to head off deviations that might come from hitting voids. That, he says, made it ideal for the client’s dam maintenance needs. The rig also features a rod handler they call the “Rodbot,” which he says has gotten the interest of potential customers in mining, oil and gas.
We had Dalrymple on our Drilling In-Site video and podcast series to discuss the rig and how it performed in the field. This is an edited summary of our talk. Click here to see the full video, or here to listen to the podcast.
Q. Describe how MEDATech Engineering and Borterra became part of this project.
A. The customer in this case is Alabama Power, which is a division of the Southern Company a large utility down in the southern States. They were customers of Cubex … that then became Sandvik. Their Logan Martin power dam operation had a Cubex QXW, which is a self-contained water hammer in-the-hole (ITH) drill rig. It’s got rods on board. It’s got rod handling. It’s ideally suited for doing dam rehab work. These guys used it for drilling grout holes, which meant installing casing down around 100 feet and then drilling through it down to up to 600 feet.
As part of their planning process for the dam, they occasionally needed core sampling done but the QXW couldn’t do the core sampling. They couldn’t really justify a second rig, so they would just contract out the core sampling. The local company that made the most sense to them economically was one that did it using sonic technology.
When their rig got, you know, a little long in the tooth the guys put together a group and they created a big wish list of what they wanted in the replacement drill rig. This list included being able to store 600 feet of pipe on board, as well as casing. They wanted the capability of using 20-foot rods as well as 10-footers, because the Cubex could just do 10-footers. They also needed to match the capabilities of being able to drill off axis in both planes up to 15 degrees in all directions, and they needed a slideover because in their application they often come back and revisit holes and they have to realign. On top of this, they wanted to be able to do their own core sampling so they can do it on their own schedule and they’re not stuck to the schedule of the contractor, when he’s available. Then, as a further item on their list, they wanted to be able to record all their drilling data so they could combine that with their core sampling and further enhance the 3D map of the rock structure that we’re dealing with.
So they went shopping and quickly found out that no one made such a versatile rig. In fact, they said that they really couldn’t find any two rigs they would buy that would do everything they wanted. The Geostructural Services team at Southern is a pretty bright, determined group. Their supervisor, a gentleman named Eric Manning, is an engineer himself and, by his own admission, he’s always looking to push for improvements in technology in his industry. He knew what they want to do is possible. They just had to find someone who can make it happen. Eric found us at MEDATech and the rest is history. We delivered the rig in mid-2020 … and it does everything on their wish list and maybe even a few extra things.
Q. Why these two technologies, and these two technologies together? What was the thinking behind putting them together, particularly for dam work?
A. Southern’s like any other drilling operation. What everyone really wants is to drill faster, straighter and cheaper. In addition they want, in their case the ability, to take core samples and record drill data. The Wassara hammer ITH … is also known for speed and accuracy through rock. It beats compressed air on both fronts. You know, especially with these guys, they had a lot of fractured ground and stuff like sticking their bit was a big deal. The ITH really made sense for them.
Their experience with getting various coring contractors on site pushed them toward sonic because it was doing the trick and it was, like I said, faster and cheaper than what they’re used to. Sonic’s not new technology. It has been around a long time, but I think it really hasn’t got as much recognition over the years. It’s starting to become more popular these days.
With the WS 6000, the drill rig produced, they can switch back and forth between these two technologies. It just gives the operator more tools to overcome his ground conditions to do his job. In reality, we’re only just starting to see the potential of it. Southern is still in the discovery stage. They’ll undoubtedly drive their casing down using sonic because it just flies through the overburden. Once they get there, they can keep using sonic to drill through the rock, but they probably won’t because water hammer is what they know works faster. But along the way if they ever get stuck they can always just switch back and turn on those sonic vibes. They’re strong and they’ll unstick their bit quicker than they ever could have with a traditional water ITH drill. Then, at the same time, if they’re hitting something that’s unusual and they want to know what they’re into, they can pull their string out and send down a coring barrel and take a core sample. … Ultimately, having both these drilling technologies available will let them drill faster, straighter and cheaper.
Q. How many individuals are working on this rig? What does the drill crew look like?
A. It is designed for a one-man operation. When they’re sampling, they don’t have to, but they’ll often have a second guy recovering the samples. … We’ve given them a remote control so a single operator can align the sample bags and rattle his sample out into the bag himself. But, a lot of times, it’ll be done probably with two people, in which case we’ve set up the controls so that the remote control has full control. The guy who has his hands closest to the thing can’t be overridden by someone who accidentally hits a joystick or something like that in the up in the drill rig, if that makes sense. Most likely, in that case, it will be two-person operation. The guy who uses remote control, he’ll tilt the head and rattle a sample out of the coring barrel. He’ll label it, put on a rock. Then the other guy will take over and get down for the next sample.
Probably, they [the customer] will do it with two, and that’s what they’ve indicated to us. But the controls are set up so a single guy could do it. He would trip his rods out with his core barrel full — you know, when you’re using 20-foot rods and the Rodbot, you can trip out, pretty easily — and then he could jump out and run around and rattle out his core sample. If you wanted to, you can use the remote control, but I don’t think they’ll do that. I think they’ll have two guys.
The Full Interview
We interviewed Scott Dalrymple for episode 25 of our Drilling In-Site series. In addition to these questions, our talk covered borehole integrity, safety, more on the Rodbot and other topics. See the full conversation at www.thedriller.com/insite, or listen to the podcast version at www.thedriller.com/insite-podcast. Episodes also in Apple’s Podcast store. Search Drilling In-Site and tap Subscribe.
Working on an interesting project or have industry wisdom to share? Email verduscoj@bnpmedia.com to be considered for a guest spot on Drilling In-Site.
Looking for a reprint of this article?
From high-res PDFs to custom plaques, order your copy today!