Five Most Common Drilling Methods Used in Oil and Gas Exploration
Percussion or Directional Drilling? Geology, Goals Guide Choices
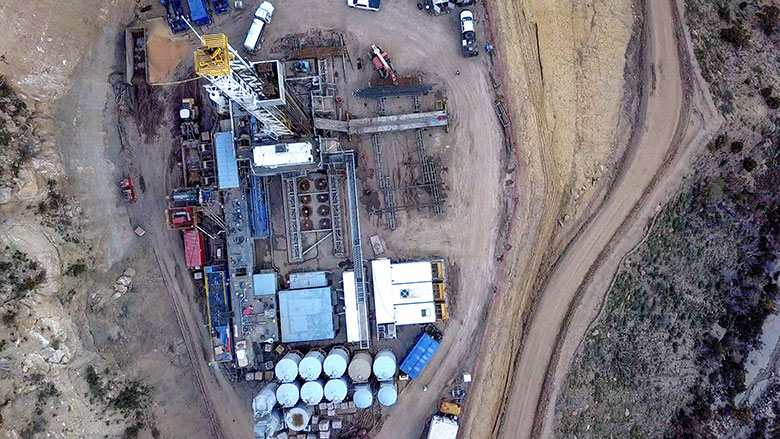
Oil and gas exploration use several drilling methods and platforms based on the formations, geographic location, soil type and other factors. Here are five of the most common drilling methods used in extracting oil and gas:
- Percussion or Cable Drilling
- Rotary Drilling
- Dual-Wall Reverse-Circulation Drilling
- Electro-Drilling
- Directional Drilling
Percussion or Cable Drilling
Percussion drilling, a commonly used manual drilling technique, employs a hammering bit attached to a long cable lowered into a wide-open hole. The technique is also known as cable drilling, wherein the driller uses a tripod to support the tools. Going back and forth with the bit loosens the soil in the borehole, which is then extracted with a bailer. At intervals, the operator removes the bit while the cuttings are suspended in water, which is then pumped to the surface and removed. A steel casing helps prevent the hole from collapsing down temporarily and also to safeguard groundwater against contamination. Drillers remove the temporary setting after a permanent screen and casing are installed.
This type of drilling is perfect for unconsolidated and consolidated formations including sand, silt, sandstone and even gravel. Manual percussion can reach depths of about 25 meters.
Rotary Drilling
Companies often deploy rotary drilling techniques, especially for exploratory and production wells that can boast of depths that exceed 5 miles below the ground.
Click here to learn more about oil & gas drilling
In this method, lightweight drills are used to drill low-depth wells on land. Rotary mobile and floating drills of various sizes are then used for drilling exploration wells. The equipment mounts on a platform with a 40-meter-high derrick. The setup consists of a rotary table, a handy engine, mud mixer and an efficient injector pump. It also includes a winch and 27-meter-long pipe sections. The rotary table directs the square kelly, which connects to the drilling pipe. The mud swivel on the pipe subsequently connects to blowout preventers. The pipe rotates at a velocity of 40 to 250 rpm with the drill made of drag bits, sharp cutting edges or rolling cutters with strong teeth.
Fluid circulation that gets inside the pipe removes the cuttings. Air-based fluids have faster penetration rates than water-based ones. A drag bit is useful in this scenario to penetrate unconsolidated sediments, while the roller bit can drill through consolidated rock. The overall rotation speed of the drill can be increased or decreased depending on the hardness of formation material.
Dual-Wall Reverse-Circulation Drilling
Dual-wall reverse-circulation, itself a type of rotary drilling, involves two concentric drill pipes creating a controlled flow. Drilling fluid pumps through an outer swivel to reach the bottom of the bit and then ricochets upward into the main pipe. All cuttings are carried upward through an internal pipe with the help of the surface swivel. The method allows for geologic sample collection, with samples usually delivered through the cyclone created at the surface. The method is compatible with both rotary drilling and percussion drilling methods. The fluids circulate within a controlled space and all cuttings can be recovered any time.
The method is applicable for all types of geologic formations and does not require surface casing, too.
Good sample recovery is one of the main strengths of this method. The method also allows for fast penetration in alluvial or fissured rock. Also, it does help in delivering an accurate estimate of aquifer yield from the depths of the formation.
Electro-Drilling
In this method, rotary tables, winches and the like are driven by electric motors, thus leading to better flexibility in operations (along with the potential for remote-controlled drilling). These drills are newer methods of oil and gas exploration. They provide more direct power to the drill bit by connecting the motor above the bit, below the hole.
The electro-drilling system has proven successful in complex geological conditions that demand the use of weighted mud or mud mixtures. Electro-drilling has made its presence felt in various places including Turkmenistan, Azerbaijan and Ukraine, which are keen to implement electro-drilling widely to boost savings in energy and material usage.
Combining the advantages of rotary and hydraulic-motor methods, this method involves a big range of drill-bit rotational speeds. This method can also use different borehole cleaning agents. One can even implement controlled drilling of deviated boreholes with this method.
Directional Drilling
Directional drilling is actually an extension of the rotary drilling technique. Operators guide the drill on a curved path with the deepening of the hole. Directional drilling can help oil explorers reach deposits that cannot be extracted by vertical drilling. This method saves drilling companies money, since several wells can kick off from a single platform. This also allows one to tap into undersea reservoirs, by using computers to guide the automatic drilling machines, without connecting and disconnecting sections.
Some other drilling methods include abrasive drilling that makes use of an abrasive material for driving pressure to cut through the substrata, and explosive drilling and flame piercing, two more methods that are used in some drilling scenarios.
Looking for a reprint of this article?
From high-res PDFs to custom plaques, order your copy today!